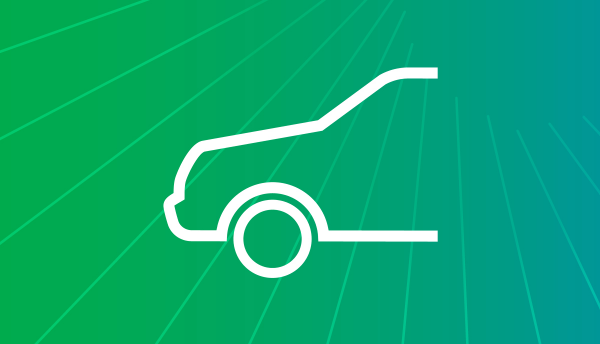
Magna will establish a new aluminium casting facility in Telford, United Kingdom, to supply aluminium castings to Jaguar Land Rover. The new facility will spread over a 225,000-square feet area and employ around 295 people at full capacity. The construction of the facility is expected to begin in autumn of 2016 and production will start in 2018, according to the company.
Aluminium use in light vehicles is expected to increase over the next decade as reducing the weight of bulky pick-up trucks and SUVs becomes a necessity. Aluminium is more expensive, but is around a third the weight of conventional steel. Rolls-Royce has recently announced that it has started testing the aluminium space frame architecture that will be used for its new generation of vehicles. Novelis has also said that it will be supplying high-strength, military-grade aluminium for Ford’s upcoming F-series Super Duty as well as the Ford F-150 pickup.
Although there have certainly been several impressive successes with largely aluminium bodies, and the use of aluminium in certain applications such as engine blocks and heads is almost universal, at least in the developed world, steel has been far from usurped. The emergence of advanced, complex phase, high strength steels and the industry’s success with hot stamping has given steel a renewed dynamism and optimism for the future. One recent example of suppliers’ investment in this area is Kobe Steel and Thailand’s Millcon Steel’s 50:50 joint-venture, set up to supply special grade steel to the automotive industry in Thailand.
Increased aluminium content needed to meet EU and US targets
The director-general of industry body European Aluminium Gerd Gotz has said the aluminium manufacturers in the region will receive a boost over the next few years as car manufacturers increase the content of aluminium components and structures as they look to save weight in order to meet stricter emissions regulations. According to a Reuters report, the aluminium industry has forecast that aluminium content will rise from an average of 140kg per car from 2012 to 180kg per car by 2020, with the particular long-term growth areas in terms of components and structural components coming from rolling sheet and extruded components. Speaking at an industry conference Gotz said, "This will be the growth engine of the aluminium downstream industry." He also added that the material was inherently more environmentally friendly than steel. He said, "The cars will not end up in a landfill anymore and you will be able to re-use the aluminium again and again."
A key driver for the increased use of aluminium in the future will be the more stringent emissions regulations that the carmakers face in both Europe and the US through the CAFE regulations which will put fleet average fuel economy at 54.5 mpg by 2025. In Europe the measurement is based on emissions and a weight equation based on the "limit value curve", with the EU mandating fleet average is to fall to 95g/km by 2021. Interestingly it is the US where the automotive application aluminium manufacturers see most potential, something evidenced with large-selling models like the new Ford F150 truck featuring an aluminium construction Gotz added, "Mass-based regulation in Europe is not giving the same incentive for light weighting as in the US. When you come to a footprint-based regulation you really bring down the CO2 curve in both weight and engine efficiency," he said, adding that the industry body wants the footprint model adopted in Europe.