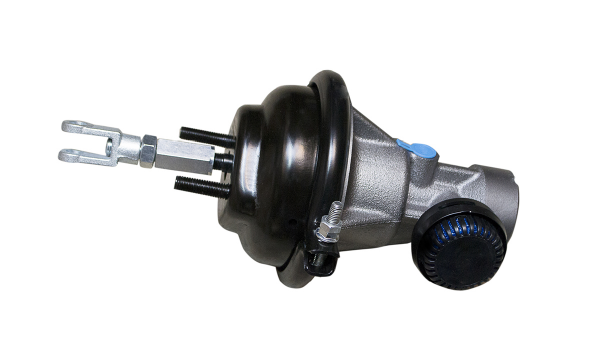
Germany-based GKN Sinter Metal has started mass-scale ‘additive manufacturing’, commonly known as 3D printing, of precision parts for engines and transmissions at its plant in Radevormwald, Germany, the company announced in a press release on 11 November. The company installed a new additive manufacturing machine called the ‘MetalFAB1’, which it claimed is the first ever employed in the automotive industry. The MetalFAB1 to produce small and medium-sized series of complex automotive components for the original equipment and replacement parts markets.
Significance: Additive manufacturing is used to build 3D parts by adding layer-over-layer of material. Additive manufacturing uses many technologies including subsets like 3D printing, rapid prototyping (RP), direct digital manufacturing (DDM), layered manufacturing and additive fabrication.
According to the company, the MetalFAB1 can simultaneously print hundreds of parts in one batch on a single build plate. “depending on how many data sets we feed into the MetalFAB1, these can be 300 identical or 300 different parts. This gives us unprecedented production capacity and flexibility,” said Dr. Simon Hoeges, GKN additive manufacturing manger. The machine which is 6.5 meters long, 1.9 meters wide and2.5 meters tall has an integrated and automated 3D printer.
While additive manufacturing has been used in industrial applications previously, mass production of such products is still not widely practiced. The company said that most of the leading automakers and system suppliers are customers for the small and medium-sized series of complex automotive components.